Make a Small Pallet Shed: A Beginner-Friendly Guide to Backyard Storage

Make a Small Pallet Shed: A Beginner-Friendly Guide to Backyard Storage
So, you've got a pile of stuff taking over your garage, and the thought of another overflowing storage unit makes your wallet weep? I get it. Building a small pallet shed is a fantastic way to reclaim some space, save a ton of money, and even have a bit of fun in the process. And the best part? It's way easier than you think, even if you've never picked up a hammer before. This guide will walk you through building your own tiny backyard haven, step-by-step.
Planning Your Pallet Paradise: Before You Even Think About a Hammer
Before you dive headfirst into this project (trust me, I've been there!), take a minute to plan things out. This will save you headaches and potentially a few bruised knuckles down the line.
Choosing Your Pallets
Not all pallets are created equal. You'll need to find pallets that are sturdy and free from rot, mold, or significant damage. Look for heat-treated pallets (stamped with "HT") rather than those treated with methyl bromide (MB), as the latter is a pesticide. Ideally, you want pallets that are relatively clean and in good condition.
Tip: Check with local businesses â" grocery stores, breweries, or even construction sites â" they often have pallets they're happy to get rid of.
Designing Your Shed
How big do you need your shed to be? Think about what you'll be storing. A small shed (say, 4ft x 4ft or even smaller) is perfect for tools, gardening supplies, or extra firewood. Larger projects will, of course, require more pallets and more planning.
Sketch out a basic design. You don't need to be an architect; a simple drawing will help you visualize the size and shape. Consider features like a door, a small roof overhang, and ventilation.
Gathering Your Materials & Tools
Beyond the pallets themselves, youâll need a few essential supplies. This list will give you a good starting point, but you might need a few extra things depending on your design.
- Screws: Plenty of long, exterior-grade screws. Galvanized screws are a great option.
- Hammer (optional): If you prefer to use nails instead of screws.
- Drill/Driver: Essential for driving in all those screws efficiently.
- Measuring Tape and Pencil: Accuracy is key.
- Level: Makes sure your shed stands straight.
- Safety Glasses and Gloves: Protect those peepers and hands.
- Roofing Material: Consider corrugated plastic, metal roofing sheets, or even tarps for a budget-friendly option. The choice depends on your climate and budget.
- Optional: Plywood or other sheeting for walls (for a more enclosed shed)
Building Your Pallet Shed: Let's Get Our Hands Dirty
With your plan and materials ready, let's start building!
The Base
Start by laying down a base of pallets to create the floor of your shed. You can arrange them to form a square or rectangle, depending on your design. Make sure theyâre level and secure. You might want to use longer screws to connect the pallets together for extra strength.
The Walls
Next, construct the walls using additional pallets. Depending on the size of your shed, you'll likely need multiple pallets per wall. Remember to keep things level and secure with screws. If you want a more enclosed shed, you can add plywood or other sheeting between the pallets. This will make it more weather resistant and also provide a more finished look.
The Door
To add a door, carefully cut or break apart a section of a pallet (carefully consider where you're cutting to ensure it remains sturdy). You can use hinges to attach the door to the shed's frame. A simple latch or hook and eye will keep it secure.
The Roof
For the roof, you can use more pallets positioned to create a simple lean-to style, or build a more complex gable roof if you're feeling ambitious. Remember to secure the roof firmly to the walls. Once the frame is complete, add your chosen roofing material. This is where your creativity can really shine. A simple tarp will do the job, but a more permanent solution like corrugated plastic or metal sheets will provide more weather protection.
Finishing Touches & Considerations
Once the structure is complete, you can add finishing touches to personalize your shed. Consider painting it to match your backyard aesthetic, adding a small window for ventilation, or attaching a simple shelf inside for better organization. You might want to consider adding a layer of sealant or weatherproofing to protect the wood from the elements. And remember â" this is YOUR shed! Let your creativity run wild.
Frequently Asked Questions (FAQs)
Here are some common questions I get asked about building pallet sheds:
How long does it take to build a pallet shed?
The time it takes depends on the size and complexity of your shed. A simple, small shed can be built in a weekend, while a larger, more complex design might take a few days. Itâs a project that can be done gradually over several days/weeks if your time is limited.
Are pallet sheds weatherproof?
The weatherproofing depends on your design and materials. A basic pallet structure won't provide much weather protection. Adding plywood between pallets, a proper roof, and sealant will greatly improve its weather resistance. Even the best pallet shed will still benefit from occasional maintenance to prolong its lifespan.
How much does it cost to build a pallet shed?
The cost is surprisingly low! The primary expense will be screws, roofing material, and any additional materials like plywood. If you find free pallets, your costs might only be for fasteners and a roof covering â" quite a cost saving compared to a pre-built shed!
What kind of permits do I need?
This varies by location. Small shed projects like this often don't require permits, but it's always a good idea to check with your local council or planning department to be sure. Better safe than sorry.
Can I use treated pallets?
While you can, it's generally best to avoid pallets treated with methyl bromide (MB) due to the potential health hazards. Heat-treated pallets (HT) are safer and readily available.
Building a pallet shed is a rewarding project that combines creativity, resourcefulness, and a touch of DIY magic. With a little planning and effort, you can have your own personalized backyard storage solution in no time. So grab those pallets and let's get building!
DIY Lean-To Shed Build: Step-by-Step Guide for Building with Pallets

Building a Lean-To Shed from Pallets: A DIY Adventure
Hey there, fellow DIY enthusiasts! So you're looking to build a lean-to shed, and you're thinking of using pallets? Fantastic! It's a super budget-friendly and surprisingly rewarding project. This guide will walk you through the whole process, from gathering materials to the final touches. Let's get started!Phase 1: Planning and Preparation â" The Foundation of Your Project
Before you even think about hammering a nail, you need a plan. Trust me, this makes the whole process way smoother.Choosing Your Location
First things first: where's your lean-to going to live? Consider these factors:
- Sunlight: Do you need shade or sun?
- Accessibility: Will you need easy access with a wheelbarrow or other equipment?
- Ground Conditions: Is the ground level? Will you need to do any leveling?
- Existing Structures: Is there a wall or fence you can lean it against?
Once you've chosen the perfect spot, clear the area of any debris, grass, or anything else that might get in your way.
Gathering Your Materials
This is where the fun (and maybe a little scavenging) begins! You'll need:
- Pallets: The number depends on the size of your shed. Aim for sturdy pallets in good condition. Check local businesses â" many are happy to give away old pallets.
- Post Mix Concrete or other stable base: For a solid base. The amount depends on the size of your shed.
- Wood screws: Various sizes, depending on the wood thickness.
- Hammer and Nails (optional): If you prefer nails over screws.
- Measuring tape and level: Essential for accuracy.
- Saw (circular saw recommended): For cutting pallets to size.
- Drill: For pre-drilling holes (recommended to prevent splitting wood).
- Safety Glasses and Gloves: Always prioritize safety!
- Roofing Material: Tarpaulin, corrugated metal sheets, or even recycled roofing materials will work. Consider weather resistance.
- Optional: Pressure-treated lumber for additional support, paint or sealant for protection.
Preparing Your Pallets
Before you start building, inspect your pallets carefully. Remove any loose nails, broken boards, or anything that might compromise the structure. You might need to disassemble some pallets and reuse the wood for specific parts. Clean them thoroughly.
Phase 2: Construction â" Building Your Lean-To
Now comes the exciting part! This is where you transform your pile of pallets into a functional shed.Creating the Base
Your base needs to be sturdy. You can either create a concrete slab or use other stable base materials like compacted gravel and pavers. Mark out the dimensions of your shed on the ground and create the base according to the chosen material.
Building the Frame
This is where youâll use your pallets. Begin by assembling the back wall. You might need to cut and adjust pallets to fit your desired height. Securely fasten them together using screws, creating a sturdy and plumb structure. Repeat this process for the side walls, attaching them to the back wall.
Remember, you're building a lean-to, so one side (usually the front) will remain open unless you decide to partially enclose it with more pallets. If you are using pressure treated lumber, this is a good point to incorporate them for greater stability.
Adding the Roof
The roof structure needs to support the chosen roofing material and be strong enough to withstand the elements. You can create a simple angled roof using more pallets. Ensure the angle is steep enough for water to run off easily. Secure the roof structure firmly to the frame.
Attach your chosen roofing material. Make sure it overlaps sufficiently to prevent leaks. For a tarp, use strong ropes or straps to secure it firmly to the frame.
Phase 3: Finishing Touches â" Making it Your Own
Securing Everything
Once your basic structure is complete, go back and check all your fastenings. Make sure everything is securely attached to prevent damage from wind or other weather conditions. Consider adding additional bracing for extra stability.
Adding Finishing Touches
This is where you can personalize your lean-to! Consider adding:
- A door: Even a simple latch will add security.
- Shelving: Maximize storage space.
- Paint or sealant: Protect the wood from the elements and add a splash of color.
- Lighting: If you'll be using the shed at night.
Commonly Asked Questions
Q: How long does it take to build a pallet lean-to shed?
A: This depends on the size and complexity of your shed, your experience, and the number of people helping. A small, simple lean-to could be built in a weekend, while a larger, more complex one might take several days or even a week.
Q: Are pallets safe to use?
A: Yes, but always inspect them carefully before using them. Remove any loose nails, splinters, or anything hazardous. Consider using gloves and safety glasses throughout the project.
Q: What kind of roofing material is best?
A: Tarpaulins are affordable and easy to install but don't last as long. Corrugated metal sheets are more durable but require more work to install.
Q: Can I build a lean-to shed against any wall?
A: It's best to lean it against a sturdy wall that can handle the extra weight. Avoid leaning against walls made from lightweight materials.
Q: What if I donât have any experience in construction?
A: Don't worry! This project is relatively straightforward. Just take your time, follow the instructions carefully, and donât be afraid to ask for help if you need it. There are plenty of online resources and videos that can assist you.
There you have it! Your guide to building a fantastic lean-to shed from pallets. Remember to always prioritize safety and have fun with it. Happy building!DIY Pallet Shed Plans: How to Build a Shed with Recycled Pallets

DIY Pallet Shed Plans: How to Build a Shed with Recycled Pallets
Constructing a shed from recycled pallets offers a cost-effective and environmentally conscious alternative to traditional shed construction. This comprehensive guide provides detailed instructions and considerations for building a durable and aesthetically pleasing pallet shed. While seemingly simple, careful planning and execution are crucial for a successful outcome.
I. Planning and Preparation
Before commencing construction, meticulous planning is paramount. This phase encompasses several key steps that will significantly impact the final product's quality and longevity.
A. Site Selection and Preparation
The chosen location must be level, adequately drained, and offer sufficient space for construction and future access. Consider proximity to power sources if electrical components are planned for the interior. Clear the area of vegetation, debris, and any potential obstructions. A slight slope to facilitate water runoff is beneficial. Mark the shed's dimensions using stakes and string to ensure accurate placement.
B. Pallet Assessment and Selection
The success of the project hinges on the quality of the pallets used. Source pallets from reputable sources, ensuring they are free from rot, significant insect infestation, and hazardous materials. Inspect each pallet meticulously for damage, loose nails, and splinters. Prioritize pallets of consistent size and construction for ease of assembly. Consider the type of wood; hardwood pallets will naturally offer greater durability.
Gather a sufficient quantity of pallets to cover the planned dimensions of your shed's walls, roof, and floor. It is advisable to have extra pallets on hand to account for potential damage during construction or to replace unsuitable pieces.
C. Material Acquisition and Tool Preparation
Beyond the pallets, gather necessary materials, including:
- Concrete mix or paving stones for a foundation (optional, but recommended).
- Pressure-treated lumber for the foundation frame (if using a frame foundation).
- Longer screws and nails for securing pallets.
- Wood glue for added strength and stability.
- Weatherproof sealant or paint for protection against the elements.
- Roofing materials (e.g., asphalt shingles, corrugated metal).
- Door hardware (hinges, latch, handle).
- Window frames and glass (optional).
Assemble the required tools, which include:
- Hammer
- Screwdriver (or drill with various drill bits)
- Measuring tape
- Level
- Saw (circular saw or hand saw)
- Safety glasses
- Work gloves
- Pry bar (for removing stubborn nails)
II. Construction Process
The construction process is divided into distinct stages, each requiring careful attention to detail.
A. Foundation Construction
A solid foundation is essential for a stable and long-lasting shed. Three options are common:
- Concrete slab: Provides the most robust foundation but requires more significant effort and materials.
- Pressure-treated lumber frame: A more accessible option involving creating a frame from pressure-treated lumber and filling the interior with gravel or compacted earth.
- Paving stones: A simple solution, offering good drainage, but might require more pallets to create a level floor.
Regardless of the chosen method, ensure the foundation is level and adequately sized to support the shed's weight.
B. Wall Construction
Begin constructing the walls by securing pallets together using screws and wood glue. Consider the orientation of the pallets; vertical placement often offers better structural integrity. Ensure the walls are plumb and square, using a level and measuring tape throughout the process. Disassemble and repurpose any damaged pallets. For larger sheds, consider adding internal bracing for increased strength.
C. Roof Construction
The roof design should be appropriate for the shed's size and location's weather patterns. A simple gable roof is a common and effective choice. Construct the roof frame using pressure-treated lumber or additional, sturdy pallets. Secure the roofing material according to the manufacturer's instructions. Ensure adequate overhang to protect the walls from rain and snow.
D. Door and Window Installation
Cut openings for doors and windows (if applicable) using a saw, ensuring sufficient clearance. Install the door and window frames, securing them firmly to the walls. Install the door and window hardware, ensuring smooth operation.
E. Floor Construction
The floor can be constructed using pallets, ensuring a level surface. Attach the pallets securely to the foundation. Consider adding a layer of plywood or other suitable material for a more finished look and to improve durability.
III. Finishing Touches and Maintenance
Once the basic structure is complete, focus on aesthetic and protective details.
A. Sealing and Painting
Apply a weatherproof sealant or paint to protect the wood from moisture damage and extend the shed's lifespan. Choose a color that complements your landscape and personal preferences. Multiple coats are generally recommended for optimal protection.
B. Interior Finishing
Add shelves or other internal features as needed. Consider adding insulation for temperature regulation if the shed is to be used as a workshop or storage space for temperature-sensitive items.
C. Ongoing Maintenance
Regular inspections are crucial. Address any signs of damage or decay promptly. Reapply sealant or paint as needed to maintain the shed's protection against the elements. Inspect the foundation for any settling or damage.
Building a pallet shed is a rewarding project that combines cost savings with environmentally friendly practices. By following these detailed instructions and paying close attention to detail, you can create a durable and functional storage solution that will serve you for years to come. Remember to always prioritize safety by using appropriate safety gear throughout the construction process.
DIY 12x20 Shed with Loft: Build Your Dream Backyard Retreat

DIY 12x20 Shed with Loft: Build Your Dream Backyard Retreat
Constructing a 12x20 shed with a loft offers a rewarding blend of practicality and personal accomplishment. This comprehensive guide details the process of building your own backyard retreat, from initial planning and material acquisition to the final touches and safety considerations. This project requires a significant time commitment, DIY experience, and careful attention to detail. Consult with local building codes and regulations before commencing.
Phase 1: Planning and Preparation
Thorough planning is paramount to a successful build. This phase involves several crucial steps that will lay the groundwork for your project.
Site Selection and Preparation
Choose a level, well-drained location with easy access for material delivery. Clear the area of vegetation, debris, and any underground utilities. Mark the shed's perimeter using stakes and string to ensure accuracy. Consider the impact on your property's aesthetics and proximity to neighbors.
Permitting and Codes
Check with your local building department for necessary permits and adherence to building codes. These regulations vary by location and will dictate aspects such as foundation requirements, structural integrity, and electrical and plumbing installations (if applicable). Obtaining permits beforehand prevents potential delays and fines.
Design and Material List
Detailed plans are essential. You can find pre-designed shed plans online or create your own, taking into account the loft's dimensions and desired features. This should include detailed drawings of the foundation, walls, roof, and loft structure. A comprehensive materials list, specifying quantities and types, will prevent mid-project delays. Factor in extra material for potential mistakes or unforeseen circumstances.
Essential Materials (Illustrative, adjust based on your design):
- Pressure-treated lumber for the foundation and framing
- Plywood or OSB for sheathing
- Roofing material (shingles, metal, etc.)
- Siding (vinyl, wood, metal, etc.)
- Insulation (optional, but recommended)
- Windows and doors
- Fasteners (nails, screws, bolts)
- Concrete (for a concrete foundation)
- Loft framing lumber
- Loft flooring material
- Exterior and interior paint or stain (optional)
Phase 2: Foundation Construction
A sturdy foundation is critical for the longevity and stability of your shed. Several options exist, each with its pros and cons.
Concrete Slab Foundation
This is the most robust and durable option. It requires excavating to the required depth, adding gravel for drainage, and pouring a concrete slab. Ensure proper leveling and curing time before proceeding to the next stage. This method is more labor-intensive but provides excellent stability.
Gravel Base Foundation
A simpler and less expensive option, this involves creating a compacted gravel base. This is suitable for lighter sheds in well-drained areas. However, it offers less stability and may not be suitable for all terrains or climates.
Pier and Beam Foundation
This involves setting concrete piers at specific intervals and constructing a beam framework on top. This offers good drainage and stability, particularly in areas with uneven ground. It is more complex than a gravel base but less labor-intensive than a concrete slab.
Phase 3: Framing and Sheathing
This phase focuses on erecting the shed's frame and applying sheathing.
Wall Framing
Following your plans, construct the wall frames using pressure-treated lumber. Ensure proper spacing and alignment. Install window and door openings as needed. Use appropriate bracing for stability.
Floor Framing
Build the floor frame on top of the foundation, ensuring levelness. Attach the floor joists to the foundation and wall frames. Install subflooring (plywood or OSB).
Roof Framing
Construct the roof trusses or rafters according to your design. Ensure proper pitch and support. Attach the trusses to the wall frames securely. Add sheathing to the roof to create a solid surface for the roofing material.
Loft Framing
Construct the loft framing within the shed's structure, ensuring adequate headroom and support. This typically involves installing joists to support the loft floor and building walls to enclose the loft area. Properly secure the loft framing to the main shed structure.
Phase 4: Exterior Finishing
Once the framing is complete, focus on the exterior finishing.
Sheathing and Siding
Apply sheathing (plywood or OSB) to the exterior walls and gable ends. Install chosen siding material (vinyl, wood, metal, etc.), ensuring proper overlapping and sealing to prevent water damage.
Roofing
Install the selected roofing material (shingles, metal, etc.), following the manufacturer's instructions. Ensure proper ventilation to prevent moisture buildup.
Doors and Windows
Install doors and windows, ensuring proper sealing and weatherproofing. Consider adding window trim for aesthetic appeal.
Exterior Trim
Install exterior trim around doors, windows, and the shed's perimeter for added protection and visual appeal. Consider adding fascia and soffit for a more polished look.
Phase 5: Interior Finishing and Loft Construction
Complete the interior and loft construction.
Loft Flooring
Install flooring in the loft area, ensuring secure attachment to the joists. Consider using lightweight materials to minimize the load on the structure.
Interior Walls (Optional)
If desired, add interior walls to create separate spaces within the shed. Use appropriate wall coverings (drywall, plywood, etc.).
Insulation (Optional)
Install insulation in the walls, ceiling, and loft for better temperature regulation. This is particularly beneficial if you plan to use the shed year-round.
Interior Finishing
Apply interior paint or stain, install lighting, and add any other desired interior features (shelving, electrical outlets, etc.).
Phase 6: Safety and Final Touches
Prioritize safety and add the finishing touches.
Electrical Work (If Applicable)
If adding electrical outlets or lighting, ensure proper wiring and adherence to local electrical codes. Consult with a qualified electrician if needed.
Safety Features
Install smoke detectors and carbon monoxide detectors (if applicable). Ensure adequate lighting for safety at night. Consider adding exterior lighting as well.
Landscaping
Complete any landscaping around the shed, including grading, seeding, or planting.
Final Inspection
Once complete, schedule a final inspection with your local building department to ensure compliance with all building codes.
Building your own 12x20 shed with a loft is a challenging yet rewarding project. With careful planning, attention to detail, and a commitment to safety, you can create a functional and attractive addition to your property, a space perfectly tailored to your needs and a testament to your DIY skills.
DIY Pole Barn Plans: How to Build Your Own Building

Hey there, DIY enthusiasts! Ever dreamt of having a spacious workshop, a cozy guest house, or a barn to house your prized possessions? Building a pole barn could be your ticket to realizing that dream. It's a project that might seem daunting at first, but trust me, it's way more achievable than you think. I'm here to guide you through the process, step by step, with a sprinkle of tips and tricks along the way.
Let's start with the basics:
What exactly is a pole barn?
Think of it as a sturdy, simple structure with a frame made of heavy-duty poles, usually made of treated lumber or steel. The poles are sunk deep into the ground for stability, creating a strong foundation. These poles act as the walls and support the roof. This construction style is incredibly versatile, allowing for a wide range of uses and sizes.
Why choose a pole barn?
There's a reason why pole barns are gaining popularity. Here's why they're a great choice:
Cost-Effective: Compared to traditional buildings, pole barns are generally cheaper to build. The straightforward construction and fewer materials involved make it a budget-friendly option.
Fast and Efficient: The simple design and prefabricated parts make the construction process much quicker than building a conventional structure.
Versatile: Pole barns can be adapted to various needs, from workshops and garages to storage units, stables, and even guest houses.
Durable: The strong pole foundation and sturdy construction make pole barns incredibly resilient against wind and weather.
Getting Started: Planning Your Pole Barn Project
Before diving into the details, let's lay the groundwork for a successful pole barn project:
Planning Permissions: Check with your local authorities to ensure you meet the necessary building codes and obtain any required permits.
Site Selection: Pick a flat, level spot with good drainage. Consider accessibility and proximity to utilities.
Design and Size: Determine the size and purpose of your pole barn to help you choose the right materials and design.
Materials and Tools: Make a detailed list of the materials you'll need, including lumber, fasteners, concrete, roofing materials, and any insulation or siding you might want. Don't forget the tools â" a chainsaw, post hole digger, drill, circular saw, level, and a tape measure are essential.
Foundation and Poles: Building the Backbone
Now comes the fun part, actually building your pole barn!
Digging the Holes: Use a post hole digger to create holes deep enough to accommodate the poles and ensure stability. You'll need a concrete footing for each pole, so make sure the holes are wider than the poles themselves.
Setting the Poles: Carefully lower the poles into the holes, ensuring they are plumb and level.
Pouring the Concrete: Mix the concrete according to instructions and pour it around the poles, making sure to pack it tightly.
Curing the Concrete: Allow the concrete to cure for at least 24 hours before moving on to the next stage.
Framing and Roof Construction
With the foundation in place, it's time to start framing:
Adding Horizontal Beams: Attach horizontal beams to the top of the poles, creating the framework for the roof.
Roof Trusses: Install pre-engineered roof trusses onto the beams. You'll likely need a crane or hoist to lift these into place.
Roof Sheathing: Cover the roof trusses with plywood or OSB sheathing.
Roofing: Choose your preferred roofing material and install it according to the manufacturer's instructions. Shingles, metal roofing, or even solar panels are common choices.
Walls, Doors, and Windows
Now for the finishing touches:
Wall Panels: Choose the type of wall panels you want, be it wood, metal, or a combination of both. You can also opt for insulation between the panels for added comfort and energy efficiency.
Doors and Windows: Install the doors and windows you've selected, ensuring they are properly sealed and weatherproofed.
Finishing Touches: Add the final details, such as trim, gutters, and any other desired features.
Electrical and Plumbing
Remember, a pole barn is more than just a shell. If you're planning on using it for living space or a workshop, you'll likely need electricity and potentially plumbing:
Electrical Wiring: Get a licensed electrician to install the wiring and any necessary outlets, fixtures, and switches.
Plumbing: If you need plumbing, consult a licensed plumber to ensure proper installation and code compliance.
Safety First: Protecting Your Project
Use Safety Gear: Always wear safety glasses, gloves, and sturdy footwear when working with tools and materials.
Be Cautious with Power Tools: Follow all safety guidelines for operating power tools, and never use them when fatigued or under the influence of drugs or alcohol.
Respect Lifting Limitations: Don't lift loads beyond your capacity; use a crane or hoist for heavy objects.
Work with a Buddy: It's always safer to have a helper or spotter when lifting, moving, or working at heights.
Time to Celebrate!
After all your hard work, you'll have a sturdy, versatile pole barn ready to serve its purpose. Whether it's a workshop, a storage unit, or a cozy retreat, your creation is a testament to your DIY skills and a source of pride.
Tips and Tricks:
Don't Cut Corners: Investing in quality materials and tools will save you headaches in the long run.
Take Your Time: Rushing the project can lead to mistakes.
Seek Expert Advice: If you're unsure about any part of the process, consult a contractor or experienced builder.
Enjoy the Process: Building a pole barn is a rewarding experience. Embrace the challenges and celebrate the victories along the way!
Remember, building a pole barn is a journey, not a race. Enjoy the process, learn from your experiences, and let your creativity guide you. You've got this!
DIY Pole Barn Plans: How to Choose the Right Dimensions
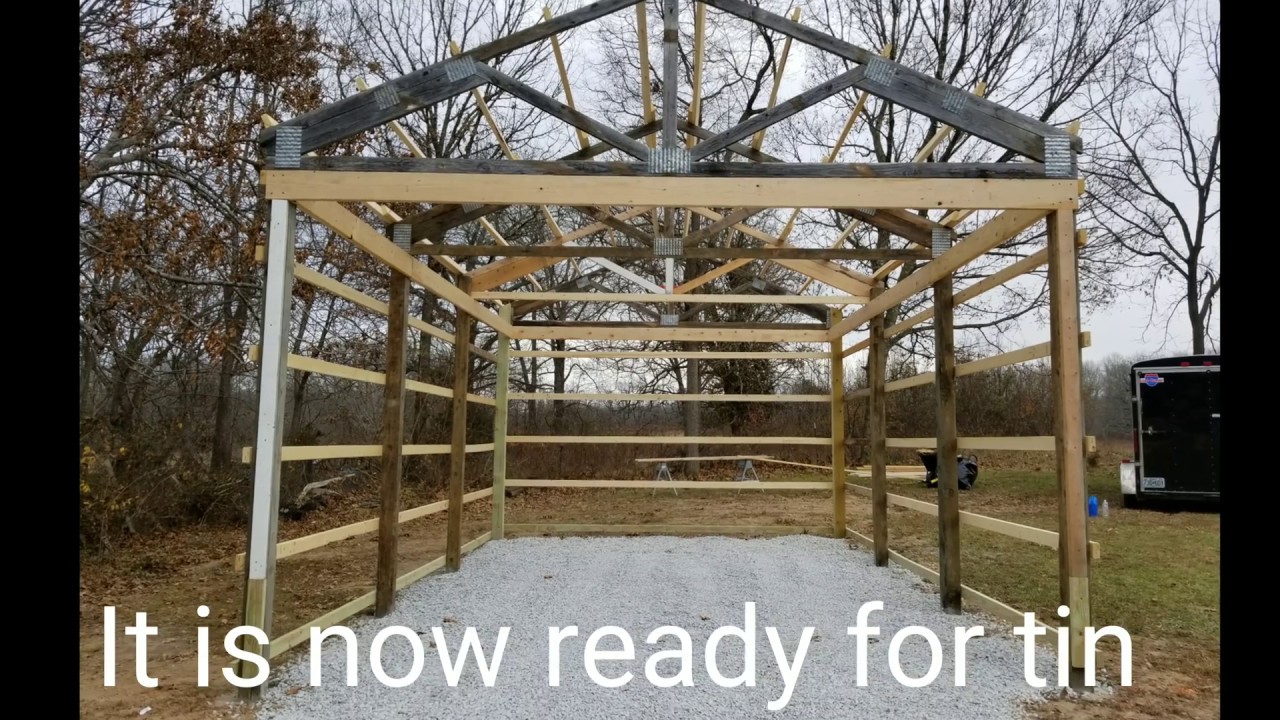
Alright, you've got the vision. A beautiful pole barn, ready to house everything from your prized car collection to a workshop bursting with creativity. But before you start digging those holes and ordering lumber, let's talk about the most crucial step: choosing the right dimensions for your pole barn.
Don't worry, it's not as daunting as it sounds. We'll break it down in a way that's easy to understand, even if you're a DIY newbie.
1. Start with the Basics: What's Your Purpose?
Think about how you plan to use your pole barn. Is it for storage? A workshop? A garage for multiple vehicles? Maybe a combination of all three? Answering this question will guide you in determining the necessary space.
Storage: Do you need a lot of floor space for large items? Consider the dimensions of the biggest things you'll be storing, and add some extra room for maneuvering.
Workshop: How much space do you need for your workbench, tools, and any equipment you'll be using? Think about how you'll be moving around the space and allow for adequate aisle width.
Garage: How many cars will you be storing? Remember to allow enough space between cars for opening doors and walking around.
2. Don't Forget the Extras:
Beyond the main purpose, there are other factors to consider that might affect the dimensions:
Future Expansion: Think about whether you might need to expand your pole barn in the future. Maybe you'll want to add a second story or a separate room. Adding some extra length or width now can save you headaches later.
Door and Window Placement: Consider where you'll need doors for access and windows for natural light. Don't forget about the size and placement of overhead doors for vehicles.
Local Building Codes: Check with your local building department to see if there are any restrictions on the size or height of your pole barn.
Cost: Remember, bigger isn't always better. Larger dimensions mean more materials and more labor costs. Balance your needs with your budget.
3. Dive into the Details:
Now it's time to get specific with the dimensions:
Width: This is the length of the side walls. Consider your vehicles' width, the width of your workbenches, and any other bulky items you'll be storing. Remember, you'll also need space for doors and windows. A standard width for a single-car garage is 12 feet, while a two-car garage is typically 24 feet. For a workshop, you might need a width of 16-20 feet.
Length: This is the distance between the side walls. Consider the length of your vehicles, the length of your workbenches, and the space you need for aisles. For a one-car garage, a length of 20-24 feet is standard. For a two-car garage, you'll need at least 30 feet. A workshop might need a length of 24-30 feet.
Height: The height of your pole barn will determine the amount of headroom you have. Consider the height of your vehicles, your ceilings, and any other equipment you'll be using. A standard height for a garage is 8-10 feet. For a workshop, you might need a height of 10-12 feet.
4. Visualizing Your Space:
To make sure you're happy with your chosen dimensions, try visualizing your pole barn in a few different ways:
Floor Plan: Draw a simple floor plan of your pole barn, outlining the dimensions, the placement of doors and windows, and the locations of your vehicles, workbenches, or other storage items.
Scale Drawing: Use graph paper or a free online tool to create a scale drawing of your pole barn. This will give you a better sense of the actual size and layout.
3D Modeling: If you're comfortable with 3D modeling software, create a 3D model of your pole barn. This can help you visualize the space from multiple angles and make sure you're happy with the overall design.
5. Don't Be Afraid to Adjust:
Remember, this is just a starting point. You can always adjust the dimensions as you go. The most important thing is to create a space that meets your needs and fits your budget.
Example Dimensions for a Multi-Purpose Pole Barn:
Let's say you want to build a pole barn that will serve as a garage for two cars, a workshop, and storage space. Here's a possible dimension breakdown:
Width: 24 feet (enough for two cars plus walking space)
Length: 36 feet (room for the cars, a workbench, and storage)
Height: 10 feet (plenty of headroom for cars and tall storage)
Additional Tips for Choosing Dimensions:
Go for the Bigger Barn: It's generally better to err on the side of a larger barn than a smaller one. You'll thank yourself later if you have more space than you need.
Don't Forget the Foundation: The size and type of foundation you choose will depend on the dimensions and weight of your pole barn. Talk to a contractor or engineer to determine the best foundation for your project.
Consult with Professionals: Don't be afraid to seek professional advice from a contractor or engineer. They can help you design a pole barn that's safe, structurally sound, and meets your specific needs.
Building a pole barn is a big undertaking, but it's also a rewarding one. By carefully planning the dimensions of your pole barn, you'll be setting yourself up for success and enjoying your new space for years to come.
How to Build a Pole Barn with Insulated Panels
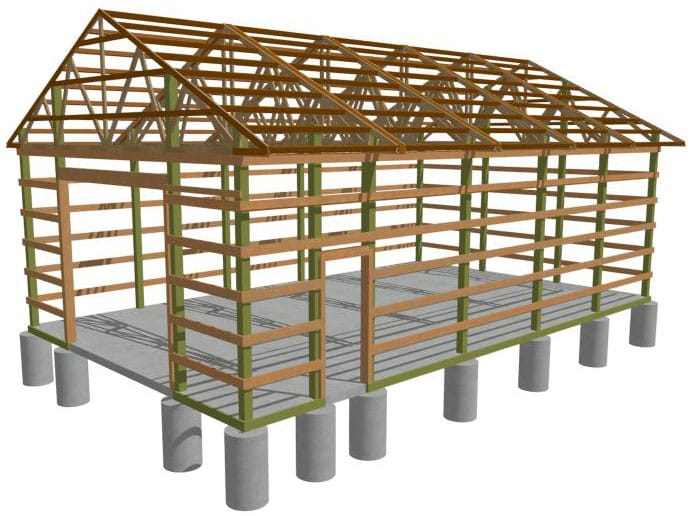
Pole barns, renowned for their versatility and cost-effectiveness, offer a practical and durable solution for a wide range of applications. Integrating insulated panels into the construction elevates the structure's functionality and energy efficiency, making them ideal for workshops, garages, agricultural storage, and even residential living spaces. This comprehensive guide provides a detailed roadmap for building a pole barn with insulated panels, encompassing every step from planning to completion.
1. Planning and Preparation:
a) Design and Layout:
Purpose and Functionality: Clearly define the intended use of the pole barn. This will guide decisions regarding size, layout, and structural requirements. For example, a workshop will need ample floor space and potentially specialized electrical wiring, while a storage barn may prioritize maximizing storage capacity.
Site Assessment: Thorough site evaluation is crucial. Consider factors like terrain, soil conditions, access roads, and proximity to utilities. Ensure compliance with local building codes and zoning regulations.
Structural Engineering: Engage a qualified structural engineer to design a plan incorporating the specific load requirements for your chosen purpose. The engineer will determine pole spacing, foundation type, and overall structural integrity.
Architectural Design: Consider the aesthetic appeal of your pole barn. Architectural elements like roof pitch, window placement, and exterior cladding can significantly influence the final look.
b) Material Selection:
Pole Materials: The most common options include pressure-treated wood, steel poles, and concrete poles. Pressure-treated wood offers affordability, while steel and concrete provide greater durability and resistance to pests and rot. Choose the option that best suits your budget and requirements.
Insulated Panels: These panels are available in various materials, including:
Foam Core: Lightweight and cost-effective, offering good insulation properties.
Fiberglass Reinforced Plastic (FRP): Strong and impact-resistant, suitable for areas prone to harsh weather conditions.
Polyurethane: Excellent thermal insulation and moisture resistance, suitable for a wide range of applications.
Metal: Durable and fire-resistant, often used for industrial and commercial buildings.
Roofing Materials: Popular options include metal roofing, asphalt shingles, and concrete tiles. Consider factors like durability, cost, and aesthetic preferences.
Doors and Windows: Select doors and windows that meet your specific needs for functionality, size, and insulation performance.
2. Site Preparation and Foundation:
Clearing and Grading: Clear the site of vegetation, debris, and any obstacles. Grade the area to achieve proper drainage and create a level foundation.
Foundation Construction: The foundation type will depend on the soil conditions and the weight of the structure. Options include:
Concrete Piers: Cost-effective and suitable for lighter structures on well-drained soil.
Concrete Footings: Stronger and more stable, suitable for heavier structures or areas with challenging soil conditions.
Concrete Slab: Provides a solid, level surface for the floor, suitable for workshops or living spaces.
Pole Installation: Position the poles according to the structural engineer's plan. Securely embed them in the foundation using concrete or specialized anchors.
3. Erection of the Pole Barn Frame:
Framing: Construct the frame using lumber or steel beams according to the engineer's specifications. Use appropriate fasteners and connectors for secure and durable connections.
Rafter and Truss Installation: Install the rafters or trusses to support the roof structure. Ensure proper spacing and alignment for optimal strength and load distribution.
Sheathing and Roofing: Apply sheathing panels to the roof frame, providing a base for the roofing material. Install the roofing system, adhering to manufacturer's instructions for optimal performance.
4. Insulated Panel Installation:
Panel Preparation: Measure and cut the panels to the desired dimensions, ensuring precise fit and minimizing waste.
Installation: Use specialized clips or fasteners designed for insulated panel attachment. Ensure proper alignment and consistent spacing for optimal performance and aesthetic appeal.
Flashing and Sealants: Apply flashing around windows, doors, and other penetrations to prevent water intrusion. Seal any gaps or joints with weatherproof sealants to maintain insulation integrity.
5. Finishing Touches:
Interior and Exterior Cladding: Apply interior and exterior cladding as desired, ensuring a smooth and aesthetically pleasing finish.
Door and Window Installation: Install doors and windows according to the manufacturer's guidelines, ensuring proper alignment and sealing.
Electrical and Plumbing: Install electrical wiring, plumbing lines, and other utilities as required, adhering to local codes and regulations.
Final Touches: Complete the project with final touches like painting, staining, or other decorative elements to enhance the appearance and protect the structure.
6. Maintenance and Care:
Regular Inspection: Periodically inspect the structure for any damage or deterioration, addressing issues promptly.
Cleaning and Maintenance: Maintain the exterior and interior surfaces by regularly cleaning and applying appropriate protective coatings.
Insulation Integrity: Monitor the condition of the insulated panels and address any damage or degradation to maintain energy efficiency.
Benefits of Insulated Panels:
Enhanced Energy Efficiency: Insulated panels significantly improve thermal insulation, reducing energy consumption for heating and cooling.
Cost Savings: The improved energy efficiency leads to lower utility bills over time, offsetting the initial investment cost.
Moisture Control: The panels resist moisture penetration, preventing damage from condensation and improving the longevity of the structure.
Sound Reduction: Insulated panels provide excellent sound insulation, creating a quieter and more comfortable environment inside the pole barn.
Versatility: Suitable for a wide range of applications, from workshops and garages to agricultural storage and even residential living spaces.
Conclusion:
Building a pole barn with insulated panels offers a combination of cost-effectiveness, durability, and energy efficiency. By carefully planning, selecting suitable materials, and following proper construction techniques, you can create a versatile and functional structure that meets your specific needs for years to come. Remember to consult with professionals for structural engineering and design guidance to ensure a safe and efficient construction project. With proper maintenance and care, your pole barn will serve as a valuable asset for years to come.